DestacadosNotas MinerasNoticias
Syntec desarrolla simulación dinámica a proyecto de expansión de gran minera del Norte del país
- Syntec logró identificar el runtime de una planta concentradora, para evaluar las capacidades del nuevo diseño, identificación de los cuellos de botella y holguras del circuito de molienda que se agregarán al proceso. “Calibrar un modelo es complejo porque debe asemejarse a lo que ocurre en la realidad», explica Javier Rodríguez, especialista en Procesos y jefe de Proyectos de esta empresa nacional.
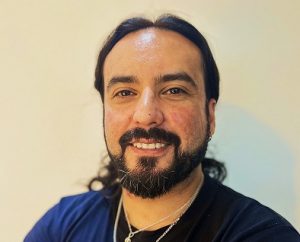
Syntec desarrolló exitosamente un nuevo servicio de simulación dinámica, el que aportó a evaluar la factibilidad de un proyecto de expansión de una gran minera del cobre, ubicada en la Región de Antofagasta, y que buscaba ampliar su vida útil.
“Se nos solicitó estudiar el runtime de la planta concentradora, para evaluar las capacidades del nuevo diseño, identificar los cuellos de botella y holguras del sistema”, explica Javier Rodríguez, especialista en Procesos y jefe de Proyectos de esta empresa nacional, que resuelve desafíos complejos y ofrece soluciones de ingeniería innovadoras, mediante estudios técnicos avanzados.
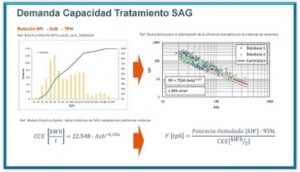
ÁREA DE PROCESOS
El experto detalla que el estudio de factibilidad tenía como objetivo confirmar si se cuenta con la capacidad necesaria para aumentar la productividad de la planta. “Entonces, había que analizar desde la perspectiva de procesos, es decir, qué equipos son los que aportan al objetivo y cuáles son los que complican los procesos. Para ello, generamos distintos casos de simulación”, precisa.
Rodríguez sostiene que la planta tiene un nivel de producción que opera con dos descargas. “Nos pidieron hacer una simulación del caso base, que es la planta actual, y así calibrar el modelo en función a lo que está ocurriendo hoy en la instalación. El proyecto suma un tercer molino, uno SAG, el que viene con sus circuitos de sistemas de molienda y chancado de pebbles. Por lo tanto, querían saber cuál era el verdadero impacto de incorporar este nuevo circuito al proceso existente y cómo elevar la producción”, revela.
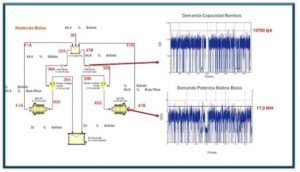
CALIBRACIÓN DE MODELO
Consultado por los desafíos que el equipo de Syntec debió resolver, el especialista indicó que están relacionados con la toma de datos. “Calibrar un modelo es complejo porque debe asemejarse a lo que ocurre en la realidad. Entonces, aplicamos nuestras tecnologías para que el modelo tomara y representara de manera realista lo que pasa a nivel de producción. Se estudiaron diferentes zonas como la alimentación, el acopio, planta de gravilla y las de cada una de las subáreas. Lo anterior nos permitió acordar con el cliente qué factor usaríamos para que el modelo representara lo que sucede en la realidad”, dice.
Realizando estas actividades, según Rodríguez, se valida la simulación. “Luego se van desarrollando simulaciones de diferentes condiciones de operación. La incorporación de este nuevo circuito de molienda y chancado de pebbles con simulación dinámica le permitió a nuestro cliente evaluar los efectos del nuevo diseño en el proceso productivo, y así contar con mayor información para tomar mejores decisiones”, resalta.
El experto asevera que el cliente quedó plenamente satisfecho con el servicio prestado por Syntec. “El trabajo se hizo en conjunto, mediante revisiones semanales para chequear y validar el avance del proyecto, y así asegurar que la construcción del modelo sea representativa de la realidad”, afirma.
“De hecho, seguimos trabajando con la gran minera, pero en otras plantas. Esto demuestra que nuestro trabajo fue bien evaluado. Lo anterior nos motiva a seguir promocionado nuestro servicio de simulación dinámica, basado en modelos matemáticos que representan el comportamiento fenomenológico, lógico y funcional de un proceso o equipo para optimizar su operatividad”, agrega Rodríguez.